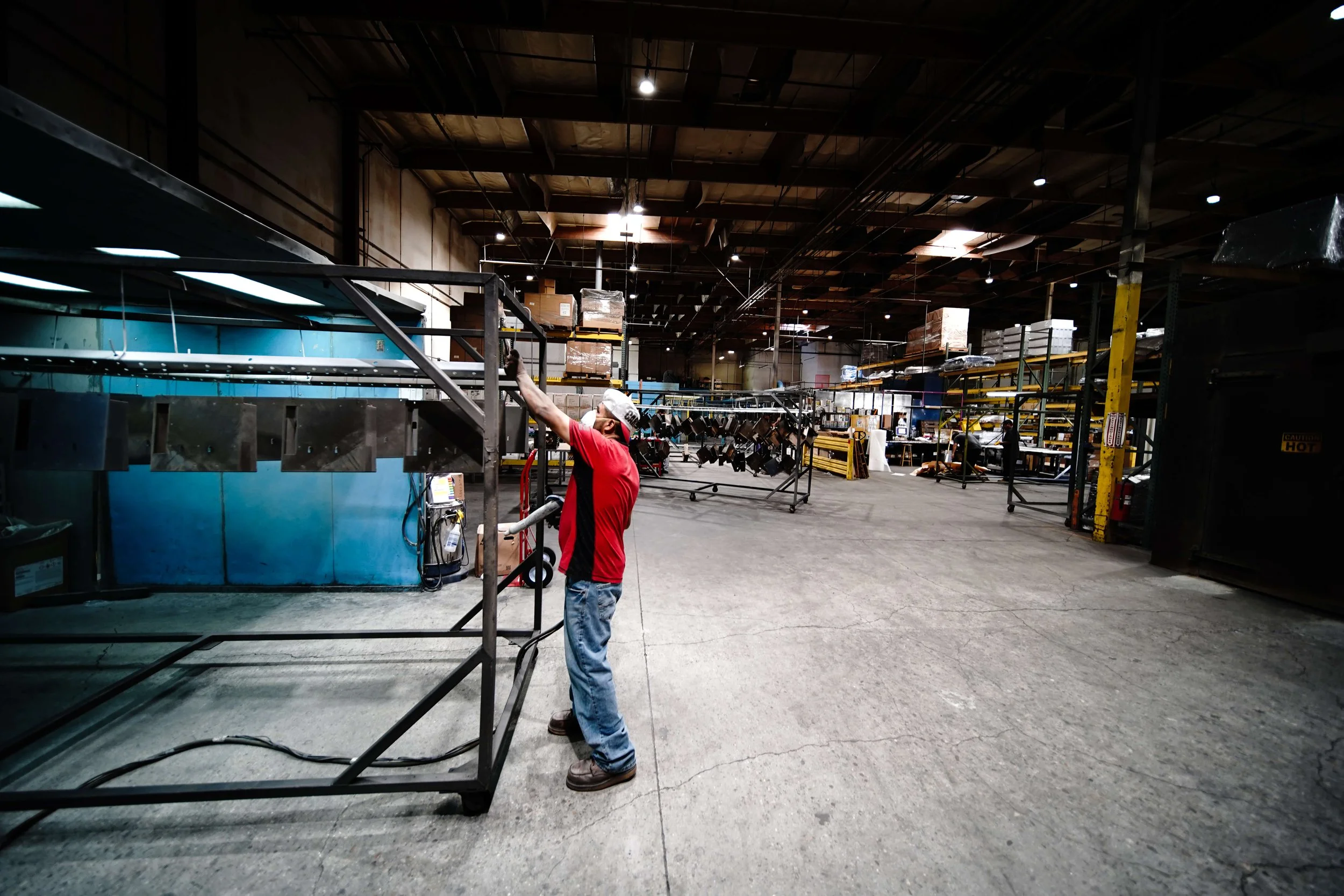
About Us
Applied Powdercoat boasts a state-of-the-art 30,000 square-foot modern facility
Our History
Applied Powdercoat, located in Oxnard, CA, was founded in 1989. The business started as a small-volume coating facility primarily servicing custom fabrication shops, low-volume sheet metal manufacturers and walk-in customers. Within 5 years, the company grew and moved into a larger space adding additional capacity, which was necessary for growing standards. Today, Applied Powdercoat serves a variety of industries, including aerospace and defense, and offers a broad scope of services to meet your project requirements.
Our State-of-the Art Facility
Our facility houses two automated lines and 3 batch systems. All systems utilize heated iron-phosphate pre-treatment and our in-house glass-bead and sandblasting.
Automated Line #1: Part sizes up to 72″ x 120″ x 30″
Automated Line #2: Part sizes up to 36″ x 40″ x 15″
Batch System #1: Part sizes up to 8′ x 8′ x 24′
Batch System #2: Part sizes up to 8′ x 9′ x 16′
Inhouse burn-off oven
Sandblast room: 8’x8’x16′
Glass-Bead Blast Cabinet: 3’x3’x3′
4 24′ Stake Bed Truck
The Powder Coating Process
Preparation
The first step to quality powder coating is surface preparation, otherwise known as pretreatment, of the metal parts to be coated. Several methods of this include solvent wiping, sandblasting or glass bead blasting, and chemical bath treatments. The most common chemical treatments are iron phosphating for steel parts, and chromate conversion for aluminum parts.
Powder Application
The second step of the powder coating process is the actual application of the powder coatings onto the parts. Using electrostatic spray guns, the powders are gently blown through the air gun, picking up a static charge, and are attracted to the grounded parts as they move through the air. The static charge is strong enough to hold the particles on the part, but not enough to disrupt the spray.
Curing
The final step to the process is curing. When the coated parts enter the 400 degree oven, the powder granules melt and flow together, and after a short period are cured. The parts are then removed from the oven and allowed to cool, after which they are fully cured and ready for packaging. At this point the powder coating process is complete and the parts are ready for use.
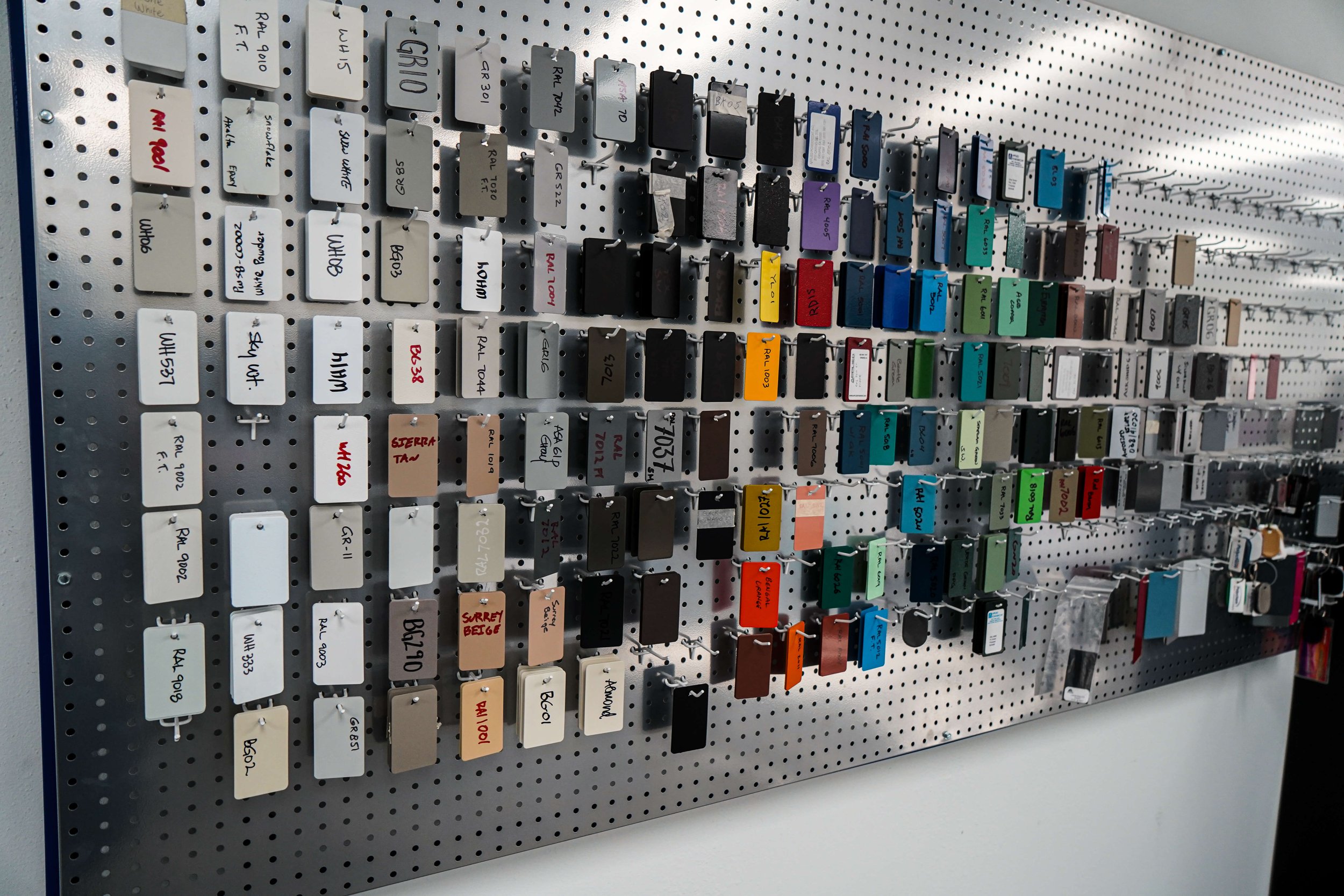